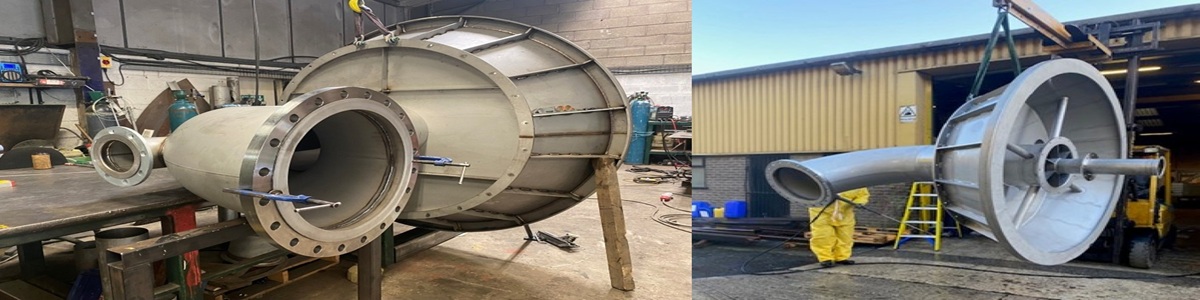
Case Studies
The Project
We were approached by a valued customer who faced the task of fabricating parts from outdated and incomplete original drawings. With a stringent deadline looming, they needed a solution that could transform these limited resources into precise electronic fabrication drawings that could then be worked on by their fabrication department.
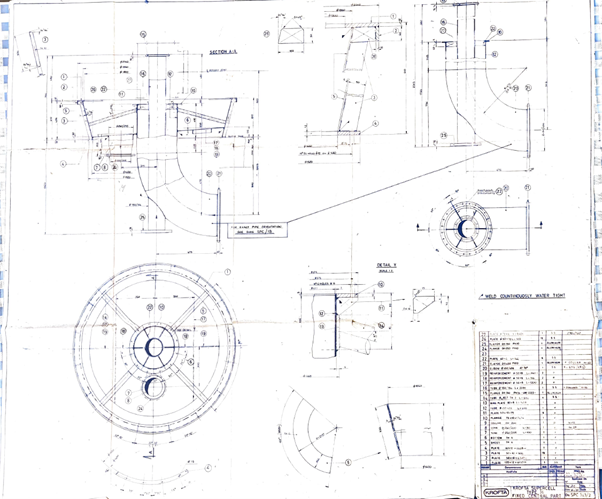
Solution
Leveraging our expertise, we undertook the challenge of breaking down the original drawings to create detailed 3D models. Using SolidWorks, we re-engineered the design into a comprehensive electronic 3D model. This allowed us to accurately extract all profile requirements and ensure that all ancillary parts positions were precisely etched, thereby minimising time during the fabrication process.
Process:
- Model Creation: We re-created the fabrication model in SolidWorks, enabling precise visualisation and extraction of profile requirements.
- Input and Contract Review: Once created the model was broken down and input into our bespoke ERP system, ensuring any information required by machine operatives was detailed on each job card. All of this then went through a secondary contract review by an experienced member of the team with over 30 years of fabrication knowledge.
- Secondary Operations: A detailed BOM was generated for our secondary operations department, ensuring all parts were accounted for and all rolling details were transferred to the operators.
Prioritisation: Parts requiring rolling were immediately prioritised and profiled, while flat products underwent deburring and packing for dispatch
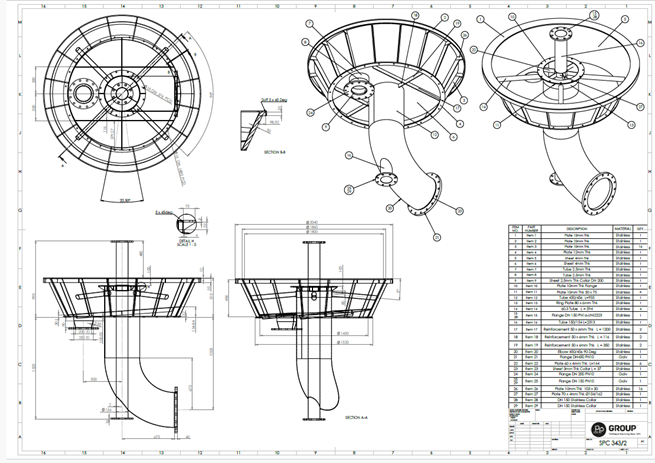
Execution: Utilising our extensive CAD expertise, multiple plate rolls, and cutting-edge fiber laser profiling technology, we managed to:
- Convert limited and outdated information into accurate, actionable 3D models.
- Expedite the profiling process to meet the client’s strict deadline.
- Ensure precision and quality, delivering correct parts the first time.
The Result
By efficiently handling the fabrication process from limited information, we enabled our client to meet their project deadline successfully. Our ability to transform outdated drawings into precise 3D models, coupled with our advanced profiling capabilities, showcased our commitment to delivering quality and efficiency even under challenging conditions.