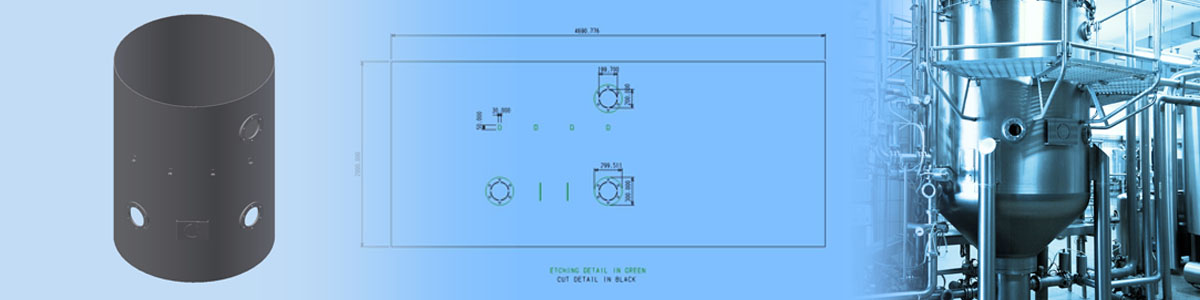
Case Studies
The Project
We were approached to manufacture several rolled, prepped and welded vessels out of 10 mm thick stainless steel plate. There were eight vessels in total, their combined weight was five tonnes and had a maximum diameter of two metres. Our team was awarded with this contract due to successfully completing a number of high-profile projects for this client.
Due to the relationship that we have with the customer, we requested access to the engineering drawings of the complete fabrication. As the drawings were examined by our technical Sales executives, it became apparent that the fabricated vessels had various apertures cut into them, primarily for outlets and man ways, as well as several brackets and lifting lugs welded to the outside of the vessel.
Armed with this additional information we contacted the client to advise that we had the ability to laser etch the positions of the brackets and lifting lugs, as well as stitch cut the apertures. We explained that this would drastically reduce our client’s manufacturing time during pre-fabrication and assembly. With the complex apertures already stitch cut in and the additional component positions marked out, a great deal of skilled fabrication time and potential errors would be eliminated.
The Result
The advice provided by our Sales team paid off, the vessels were completed two weeks ahead of schedule and the client manufactured the end product with a substantial cost saving, increasing the profitability of the project by 15%.